TEST BANK FOR Manufacturing Processes for Engineering Materials 5th Ed By Serope Kalpakjian
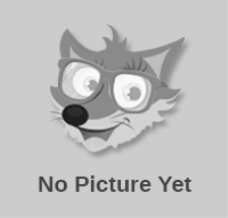
- GradeMaster1
- Rating : 1
- Grade : C+
- Questions : 0
- Solutions : 1124
- Blog : 0
- Earned : $278.60
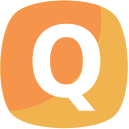
2.1 Can you calculate the percent elongation of materials
based only on the information given in
Fig. 2.6? Explain.
Recall that the percent elongation is defined by
Eq. (2.6) on p. 33 and depends on the original
gage length (lo) of the specimen. From Fig. 2.6
on p. 37 only the necking strain (true and engineering)
and true fracture strain can be determined.
Thus, we cannot calculate the percent
elongation of the specimen; also, note that the
elongation is a function of gage length and increases
with gage length.
2.2 Explain if it is possible for the curves in Fig. 2.4
to reach 0% elongation as the gage length is increased
further.
The percent elongation of the specimen is a
function of the initial and final gage lengths.
When the specimen is being pulled, regardless
of the original gage length, it will elongate uniformly
(and permanently) until necking begins.
Therefore, the specimen will always have a certain
finite elongation. However, note that as the
specimen’s gage length is increased, the contribution
of localized elongation (that is, necking)
will decrease, but the total elongation will not
approach zero.
2.3 Explain why the difference between engineering
strain and true strain becomes larger as strain
increases. Is this phenomenon true for both tensile
and compressive strains? Explain.
The difference between the engineering and true
strains becomes larger because of the way the
strains are defined, respectively, as can be seen
by inspecting Eqs. (2.1) on p. 30 and (2.9) on
p. 35. This is true for both tensile and compressive
strains.
2.4 Using the same scale for stress, we note that the
tensile true-stress-true-strain curve is higher
than the engineering stress-strain curve. Explain
whether this condition also holds for a
compression test.
During a compression test, the cross-sectional
area of the specimen increases as the specimen
height decreases (because of volume constancy)
as the load is increased. Since true stress is defined
as ratio of the load to the instantaneous
cross-sectional area of the specimen, the true
stress in compression will be lower than the engineering
stress for a given load, assuming that
friction between the platens and the specimen
is negligible.
2.5 Which of the two tests, tension or compression,
requires a higher capacity testing machine than
the other? Explain.
The compression test requires a higher capacity
machine because the cross-sectional area of the
1
© 2008 Pearson Education, Inc., Upper Saddle River, NJ. All rights reserved.
This material is protected by Copyright and written permission should be obtained from the publisher prior to any prohibited
reproduction, storage in a retrieval system, or transmission in any form or by any means, electronic, mechanical, photocopying, recording, or
likewise. For information regarding permission(s), write to:
Rights and Permissions Department, Pearson Education, Inc., Upper Saddle River, NJ 07458.
Name:Ghalib Thwapiah Email:[email protected] - [email protected] Work Phone:0041789044416
Address:Am glattbogen 112 - Zuerich - ch (Switzerland) - Zip Code:8050
specimen increases during the test, which is the
opposite of a tension test. The increase in area
requires a load higher than that for the tension
test to achieve the same stress level. Furthermore,
note that compression-test specimens
generally have a larger original cross-sectional
area than those for tension tests, thus requiring
higher forces.
2.6 Explain how the modulus of resilience of a material
changes, if at all, as it is strained: (1) for
an elastic, perfectly plastic material, and (2) for
an elastic, linearly strain-hardening material.
2.7 If you pull and break a tension-test specimen
rapidly, where would the temperature be the
highest? Explain why.
Since temperature rise is due to the work input,
the temperature will be highest in the necked
region because that is where the strain, hence
the energy dissipated per unit volume in plastic
deformation, is highest.
2.8 Comment on the temperature distribution if the
specimen in Question 2.7 is pulled very slowly.
If the specimen is pulled very slowly, the temperature
generated will be dissipated throughout
the specimen and to the environment.
Thus, there will be no appreciable temperature
rise anywhere, particularly with materials with
high thermal conductivity.
2.9 In a tension test, the area under the true-stresstrue-
strain curve is the work done per unit volume
(the specific work). We also know that
the area under the load-elongation curve represents
the work done on the specimen. If you
divide this latter work by the volume of the
specimen between the gage marks, you will determine
the work done per unit volume (assuming
that all deformation is confined between
the gage marks). Will this specific work be
the same as the area under the true-stress-truestrain
curve? Explain. Will your answer be the
same for any value of strain? Explain.
If we divide the work done by the total volume
of the specimen between the gage lengths, we
obtain the average specific work throughout the
specimen. However, the area under the true
stress-true strain curve represents the specific
work done at the necked (and fractured) region
in the specimen where the strain is a maximum.
Thus, the answers will be different. However,
up to the onset of necking (instability), the specific
work calculated will be the same. This is
because the strain is uniform throughout the
specimen until necking begins.
2.10 The note at the bottom of Table 2.5 states that
as temperature increases, C decreases and m
increases. Explain why.
The value of C in Table 2.5 on p. 43 decreases
with temperature because it is a measure of the
strength of the material. The value of m increases
with temperature because the material
becomes more strain-rate sensitive, due to the
fact that the higher the strain rate, the less time
the material has to recover and recrystallize,
hence its strength increases.
2.11 You are given the K and n values of two different
materials. Is this information sufficient
to determine which material is tougher? If not,
what additional information do you need, and
why?
Although the K and n values may give a good
estimate of toughness, the true fracture stress
and the true strain at fracture are required for
accurate calculation of toughness. The modulus
of elasticity and yield stress would provide
information about the area under the elastic region;
however, this region is very small and is
thus usually negligible with respect to the rest
of the stress-strain curve.
2.12 Modify the curves in Fig. 2.7 to indicate the
effects of temperature. Explain the reasons for
your changes.
These modifications can be made by lowering
the slope of the elastic region and lowering the
general height of the curves. See, for example,
Fig. 2.10 on p. 42.
2.13 Using a specific example, show why the deformation
rate, say in m/s, and the true strain rate
are not the same.
The deformation rate is the quantity v in
Eqs. (2.14), (2.15), (2.17), and (2.18) on pp. 41-
46. Thus, when v is held constant during de-
2
© 2008 Pearson Education, Inc., Upper Saddle River, NJ. All rights reserved.
This material is protected by Copyright and written permission should be obtained from the publisher prior to any prohibited
reproduction, storage in a retrieval system, or transmission in any form or by any means, electronic, mechanical, photocopying, recording, or
likewise. For information regarding permission(s), write to:
Rights and Permissions Department, Pearson Education, Inc., Upper Saddle River, NJ 07458.
Name:Ghalib Thwapiah Email:[email protected] - [email protected] Work Phone:0041789044416
Address:Am glattbogen 112 - Zuerich - ch (Switzerland) - Zip Code:8050
formation (hence a constant deformation rate),
the true strain rate will vary, whereas the engineering
strain rate will remain constant. Hence,
the two quantities are not the same.
2.14 It has been stated that the higher the value of
m, the more diffuse the neck is, and likewise,
the lower the value of m, the more localized the
neck is. Explain the reason for this behavior.
As discussed in Section 2.2.7 starting on p. 41,
with high m values, the material stretches to
a greater length before it fails; this behavior
is an indication that necking is delayed with
increasing m. When necking is about to begin,
the necking region’s strength with respect
to the rest of the specimen increases, due to
strain hardening. However, the strain rate in
the necking region is also higher than in the rest
of the specimen, because the material is elongating
faster there. Since the material in the
necked region becomes stronger as it is strained
at a higher rate, the region exhibits a greater resistance
to necking. The increase in resistance
to necking thus depends on the magnitude of
m. As the tension test progresses, necking becomes
more diffuse, and the specimen becomes
longer before fracture; hence, total elongation
increases with increasing values of m (Fig. 2.13
on p. 45). As expected, the elongation after
necking (postuniform elongation) also increases
with increasing m. It has been observed that
the value of m decreases with metals of increasing
strength.
2.15 Explain why materials with high m values (such
as hot glass and silly putty) when stretched
slowly, undergo large elongations before failure.
Consider events taking place in the necked region
of the specimen.
The answer is similar to Answer 2.14 above.
2.16 Assume that you are running four-point bending
tests on a number of identical specimens of
the same length and cross-section, but with increasing
distance between the upper points of
loading (see Fig. 2.21b). What changes, if any,
would you expect in the test results? Explain.
As the distance between the upper points of
loading in Fig. 2.21b on p. 51 increases, the
magnitude of the bending moment decreases.
However, the volume of material subjected to
the maximum bending moment (hence to maximum
stress) increases. Thus, the probability
of failure in the four-point test increases as this
distance increases.
2.17 Would Eq. (2.10) hold true in the elastic range?
Explain.
Note that this equation is based on volume constancy,
i.e., Aolo = Al. We know, however, that
because the Poisson’s ratio is less than 0.5 in
the elastic range, the volume is not constant in
a tension test; see Eq. (2.47) on p. 69. Therefore,
the expression is not valid in the elastic
range.
2.18 Why have different types of hardness tests been
developed? How would you measure the hardness
of a very large object?
There are several basic reasons: (a) The overall
hardness range of the materials; (b) the hardness
of their constituents; see Chapter 3; (c) the
thickness of the specimen, such as bulk versus
foil; (d) the size of the specimen with respect to
that of the indenter; and (e) the surface finish
of the part being tested.
2.19 Which hardness tests and scales would you use
for very thin strips of material, such as aluminum
foil? Why?
Because aluminum foil is very thin, the indentations
on the surface must be very small so as not
to affect test results. Suitable tests would be a
microhardness test such as Knoop or Vickers
under very light loads (see Fig. 2.22 on p. 52).
The accuracy of the test can be validated by observing
any changes in the surface appearance
opposite to the indented side.
2.20 List and explain the factors that you would consider
in selecting an appropriate hardness test
and scale for a particular application.
Hardness tests mainly have three differences:
(a) type of indenter,
(b) applied load, and
(c) method of indentation measurement
(depth or surface area of indentation, or
rebound of indenter).
[Solved] TEST BANK FOR Manufacturing Processes for Engineering Materials 5th Ed By Serope Kalpakjian
- This solution is not purchased yet.
- Submitted On 15 Nov, 2021 06:27:55
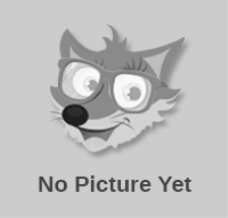
- GradeMaster1
- Rating : 1
- Grade : C+
- Questions : 0
- Solutions : 1124
- Blog : 0
- Earned : $278.60
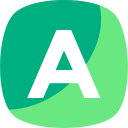
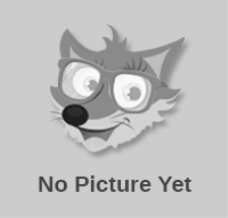
Health and Health Care Delivery in Canada 2nd Edition Test Bank
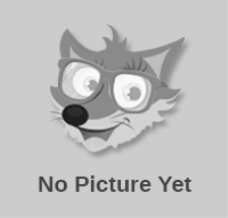
ATI Pharmacology Proctored Exam Test Bank
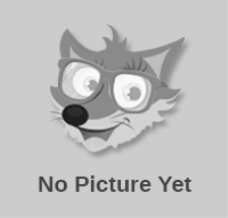
Burns Pediatric Primary Care 7th Edition Test Bank 100 % correct answers

Physical Problems, Psychological Sources Test Bank

Physical Problems, Psychological Sources Test Bank
The benefits of buying study notes from CourseMerits
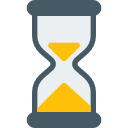
Assurance Of Timely Delivery
We value your patience, and to ensure you always receive your homework help within the promised time, our dedicated team of tutors begins their work as soon as the request arrives.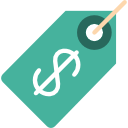
Best Price In The Market
All the services that are available on our page cost only a nominal amount of money. In fact, the prices are lower than the industry standards. You can always expect value for money from us.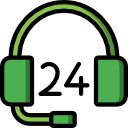